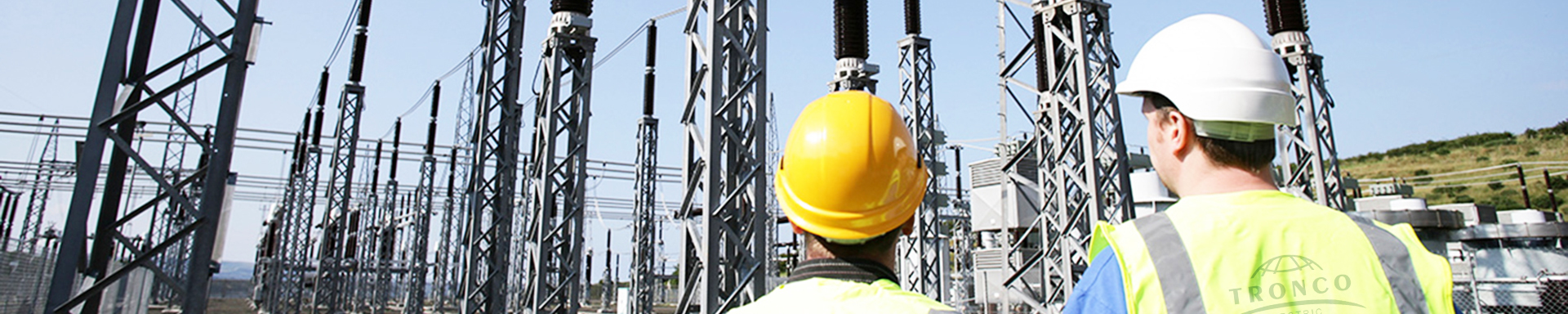
Produzione di alta qualità di isolanti in vetro temperato
2022-11-07 20:28La qualità è una misura di eccellenza ed è un punto di riferimento nel settore dell'energia elettrica utilizzando una varietà di standard nazionali o internazionali come ANSI, IEEE, IEC, ASTM, ecc. Sebbene il rispetto di questi standard sia ovviamente fondamentale, la maggior parte ha riconosciuto che gli standard in questi giorni sono arrivati a rappresentare solo i requisiti minimi di prestazioni in un'applicazione. Per questo motivo, i produttori e gli utenti stanno cercando di differenziare ulteriormente la qualità del prodotto utilizzando specifiche migliorate. La qualità è anche manifattura. A questo proposito, gli standard e il miglioramento continuo dei processi si concentrano sui controlli e sulla ripetibilità con l'obiettivo di zero difetti. In definitiva, la qualità deve rappresentare la capacità e la longevità del prodotto oltre alla conformità agli standard di base e alle specifiche del cliente.
La produzione di isolanti in vetro temperato può essere considerata come composta da due passaggi chiave: la produzione del guscio di vetro e quindi l'assemblaggio dei raccordi metallici su quel guscio. La produzione richiede attrezzature specializzate e solo pochi produttori in tutto il mondo hanno le risorse e l'esperienza per eseguire entrambe le fasi in un unico impianto di produzione. A questo proposito, è utile studiare la qualità non solo per quanto riguarda la fabbricazione del guscio di vetro temperato ma anche successivamente durante l'assemblaggio finale dell'isolatore.
Il guscio di vetro temperato costituisce l'isolante vero e proprio. Sebbene anche l'assemblaggio del raccordo e la sua cementazione siano importanti, questo guscio deve rimanere intatto per l'intera vita utile al fine di garantire la funzionalità del prodotto. Inoltre, una volta assemblato, dovrebbe essere raro il verificarsi di rotture del guscio non causate da qualche evento esterno. Ad esempio, l'aspettativa generale del settore è che meno di 1 ogni 10.000 unità installate all'anno dovrebbe andare in frantumi spontaneamente. Pertanto, l'incidenza dell'auto-frantumazione è un aspetto della produzione che la fabbrica deve sforzarsi di ridurre al minimo.
Oltre al guscio critico, i componenti hardware di un isolante in vetro temperato includono:
1. Cappellini
Il tappo in alto è un raccordo a presa in ferro duttile che è stato zincato e assemblato con un perno di bloccaggio in acciaio inossidabile.
2. Perni
Il raccordo a perno inferiore è un collegamento a sfera in acciaio forgiato che è stato zincato e rivestito con catrame bituminoso. È inoltre possibile aggiungere un collare di zinco sacrificale per prestazioni estese, specialmente in ambienti di servizio severi.
I raccordi a forcella / linguetta vengono talvolta utilizzati a tensioni inferiori.
3. Vetro grezzo e fornace
La produzione del guscio di vetro inizia con materie prime e ingredienti chiave, tra cui silice, allumina, carbonato di sodio, solfato di sodio, calcare, potassa e dolomite. Il rottame (a volte indicato come seme di vetro) è il vetro riciclato dalla produzione precedente e aggiunto a queste materie prime per garantire la coerenza da un lotto all'altro. La miscelazione di questi materiali è specifica per ciascun produttore e vede piccole variazioni negli elementi che vengono estratti da fonti locali o utilizzati nella fornace. Queste variazioni naturali nei minerali spiegano la leggera differenza osservata nella tonalità del guscio isolante in vetro.
I forni sono tipicamente di grandi dimensioni con una capacità superiore a 100 tonnellate. Per coerenza, è importante mantenere la temperatura e anche monitorare regolarmente la chimica dell'output e la miscela di materie prime che vengono immesse. Il forno è la prima possibile fonte di inclusioni - imperfezioni nel vetro che possono eventualmente causare frantumazione spontanea. Ad esempio, nel corso del tempo i mattoni refrattari possono iniziare a versare il materiale nella miscela di vetro. I forni devono quindi essere spenti per manutenzione ogni pochi anni e rivestiti.
Formazione della conchiglia
Questo avviene su una pressa automatizzata con una quantità precisa di goccia di vetro fuso inserita nella cavità dello stampo e pressata (vedi Fig. 1). Le dimensioni di ogni particolare calotta, ovvero altezza e diametro, sono definite dagli standard, ma la geometria e il profilo della calotta possono differire da un fornitore all'altro.
Processo di tempra
Dopo la formatura, il guscio subisce uno speciale processo per il quale viene trasferito dalla pressa ad una linea di tempra, passando attraverso un forno di omogeneizzazione per mantenere il vetro ad una temperatura elevata costante. La tempra del vetro si ottiene raffreddando rapidamente il vetro caldo utilizzando aria compressa in punti chiave lungo il guscio per ottenere un raffreddamento uniforme. Ciò fa sì che il vetro abbia una temperatura centrale calda ma una superficie relativamente fredda. La struttura del vetro dopo la tempra vede il centro in tensione mentre la superficie è in compressione e questo aumenta la resistenza meccanica ed elettrica oltre che la durabilità delle parti isolanti in vetro. Il raggiungimento di una qualità uniformemente elevata in questa fase critica richiede un processo di movimentazione dei materiali altamente automatizzato e attentamente controllato.
Ciclo Termico
Dopo l'indurimento, i gusci vengono trasferiti attraverso un ciclo termico prescritto, dove vengono sottoposti a shock termico con l'obiettivo di estrarre gusci potenzialmente difettosi. I gusci vengono riscaldati a circa 300°C e poi immersi in acqua fredda, abbassando di fatto la temperatura del vetro a 120°C. I gusci di vetro non sufficientemente temprati crolleranno per l'improvviso shock termico. Ogni calotta viene testata termicamente almeno una volta e, se necessario, l'intero processo può essere ripetuto. Il ciclo di shock termico è essenzialmente un controllo di qualità chiave in quanto qualsiasi guscio che si apre è un"Non andare"mentre le conchiglie che sopravvivono sono un 'Go'. Quei gusci di vetro che collassano durante il ciclo termico vengono riciclati, con frammenti raccolti e aggiunti nuovamente al processo produttivo sotto forma di rottame (seme di vetro).
Il funzionamento del forno è"24/7"e quindi più veloce del processo di assemblaggio. Per questo motivo, i gusci completati vengono tenuti in magazzino fino al momento dell'assemblaggio. Assemblaggio cappuccio e perno I gusci di vetro sono cementati nei cappucci, mentre il perno e le guaine in zinco sono cementati nel guscio con cemento alluminoso. Anche in questo caso, l'automazione viene utilizzata per garantire una quantità di cemento misurata con precisione e ottenere una tolleranza di lunghezza precisa. L'assieme cementato viene quindi indurito mediante cicli di un bagno di un'ora in acqua a circa 70°C. Dopo l'indurimento, ogni isolante in vetro temprato viene sottoposto a collaudi elettrici e meccanici di routine oltre che a controlli visivi finali.
Test elettrico di routine: flashover continuo per 4 minuti,
Test meccanico di routine: mantenuto al 50% del rating SML per>3 sec.
Su ogni lotto assemblato di isolatori vengono quindi eseguiti test di campionamento. Ciò include la verifica di tutte le dimensioni critiche, la conformità del calibro presa/sfera, la verifica del sistema di bloccaggio, il controllo della zincatura, il test M&E e il test di perforazione a impulso.
Convalida e rapporti di prova
Gli isolatori finiti sono soggetti a test di progettazione o qualificazione secondo gli standard del settore, tra cui ANSI C29-2B, IEC 60383, CSA-411-1-16 e GOST 6490-93. I clienti possono anche aggiungere ulteriori criteri di test al di sopra e al di là di questi standard alle loro specifiche per qualificare ulteriormente le prestazioni finali dell'isolante.
I rapporti di prova per ciascun modello di isolante devono essere specifici per la fabbrica in cui viene prodotto l'isolatore. Se un fornitore ha due fabbriche che producono lo stesso tipo di isolante, dovrebbero esserci rapporti di progettazione/qualificazione separati per ciascun isolante specifico per l'impianto in cui è stato realizzato. Per i prodotti assemblati in un altro luogo, i rapporti di prova per questi dovrebbero includere riferimenti a quale fabbrica ha realizzato il guscio. Se i gusci di vetro temperato provengono da due fabbriche, ciò dovrebbe richiedere rapporti di prova separati (vale a dire specifici per la fabbrica che ha prodotto il guscio).
Conclusioni
Quando si considera la qualità di un isolante in vetro temperato, la valutazione e la qualificazione devono essere approfondite e includere ogni aspetto della produzione. Dovrebbe essere prestata particolare attenzione a dove viene fabbricato il guscio di vetro temperato e anche a come viene mantenuto tale processo per evitare che gusci difettosi vengano mai utilizzati nell'assemblaggio di isolatori finiti. Questo perché, mentre l'assemblaggio del cappuccio e del perno è importante, la qualità del guscio in vetro temperato avrà un impatto maggiore sulle prestazioni dell'isolante a lungo termine. I rapporti di prova dovrebbero essere specifici per la fabbrica in cui viene prodotto l'isolante, ma dovrebbero anche fare riferimento a dove è stato fabbricato l'involucro. Ciò richiederebbe specifici contrassegni di fabbrica. Come minimo, il guscio in vetro temperato dovrebbe avere dei contrassegni stampati nel suo corpo, tra cui classificazione M&E, codice lotto di riferimento, e identificazione della fabbrica (ID). Questi contrassegni devono essere leggibili e permanenti. L'ID della fabbrica in cui è assemblato l'isolatore deve essere contrassegnato sul cappuccio dell'isolatore, anch'esso leggibile e permanente. Anche se realizzato nella stessa fabbrica, avere tali segni sia sul guscio che sul cappuccio aiuta a identificare quando il guscio è stato fabbricato e quando è stato assemblato. L'aggiunta di contrassegni identificativi di fabbrica al guscio è semplice, con un impatto minimo sul costo del prodotto, ma offre un livello più elevato di garanzia della qualità per gli isolatori. I vari standard del settore (ad esempio ANSI, IEC, CSA) non richiedono specificamente l'ID di fabbrica su una shell, ma forse dovrebbero. Anche se realizzato nella stessa fabbrica, avere tali segni sia sul guscio che sul cappuccio aiuta a identificare quando il guscio è stato fabbricato e quando è stato assemblato. L'aggiunta di contrassegni identificativi di fabbrica al guscio è semplice, con un impatto minimo sul costo del prodotto, ma offre un livello più elevato di garanzia della qualità per gli isolatori. I vari standard del settore (ad esempio ANSI, IEC, CSA) non richiedono specificamente l'ID di fabbrica su una shell, ma forse dovrebbero. Anche se realizzato nella stessa fabbrica, avere tali segni sia sul guscio che sul cappuccio aiuta a identificare quando il guscio è stato fabbricato e quando è stato assemblato. L'aggiunta di contrassegni identificativi di fabbrica al guscio è semplice, con un impatto minimo sul costo del prodotto, ma offre un livello più elevato di garanzia della qualità per gli isolatori. I vari standard del settore (ad esempio ANSI, IEC, CSA) non richiedono specificamente l'ID di fabbrica su una shell, ma forse dovrebbero.